Toy manufacturing within the Odoo ERP system offers a good solution to streamline and optimize production processes. Odoo's modules and features are for manufacturing operations, so toy manufacturers can easily manage their entire manufacturing cycle.
A fundamental aspect of managing toy manufacturing in Odoo is the creation of Bills of Materials (BOMs) for each toy. BoMs outline the required components and raw materials, along with their quantities, needed for production. Work orders are generated based on these BoMs, enabling efficient planning and scheduling of production tasks. Work orders can be selected for specific workstations or machines, ensuring a well-organized manufacturing process.
The stock management module - Inventory plays a vital role in tracking stock materials and finished goods. It facilitates automated reorder points to maintain an uninterrupted supply of materials, contributing to smoother production operations.
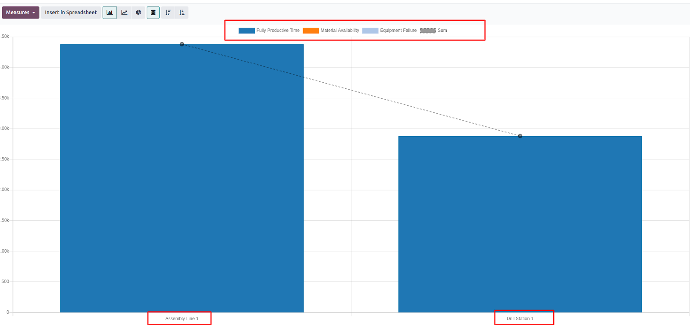
The QC (Quality control module) is linked within the manufacturing process, allowing manufacturers to uphold product quality standards. Quality tests and inspections can be set up at various production stages to ensure that toys meet safety and quality requirements.
Toy Manufacturing Setup
While creating a Finished product we have the option to add UOM, Sales price, Variants, and Routes which helps to manage multiple variants and configurable Routes & UOM for a particular toy.
We can define all this in one place for a particular product
Setting up a finished product in Odoo involves configuring several key elements that help manage and optimize the product's lifecycle from manufacturing to sales. Below is a detailed explanation of the key features involved in setting up a finished product, with an emphasis on UOM (Unit of Measure), Sales Price, Variants, and Routes.
Unit of Measure (UOM)
This feature defines the standard quantity in which a product is bought, sold, or manufactured.
Setup:
- Primary UOM: The main unit of measure for the product (e.g., pieces, kilograms, units).
- Purchase UOM: Specific to how the product is purchased if different from the primary UOM
- New UOM: Odoo handles different UOMs by deriving the value equivalent to base UOM to maintain consistency in inventory management (ex - 1kg = 1000g).
Benefits:
- Accurate inventory tracking.
- Flexible purchasing and sales options.
- Easy management of product quantities in various stages of the supply chain.
Sales Price
Definition: The sales price is the amount at which the product is sold to customers.
Setup:
- Standard Price: The base selling price of the product.
- Price lists: Different pricing strategies for different customer segments.
- Promotional offers and discounts: Apply specific discounts or promotional prices for certain periods or customer groups.
Benefits:
- A clear pricing structure for customers.
- Flexible pricing strategies to adapt to market changes.
- Improved sales control and prediction.
Variants
Variants are alternative adaptations of a product with equivalent fundamentals that deviate based on particular traits (e.g., color, size, material).
Outline:
- Traits: Delineate characteristics like color, size, and material.
- Attribute Values: Specify possible values for each attribute (e.g., red, blue for color).
- Variants Creation: Automatically create product variants based on attribute combinations
Benefits:
- Efficiently manage multiple product versions.
- Simplified product catalog management.
- Improved customer satisfaction with customizable options.
Routes
The trails that the commodity can wend its way along the supply line from procurement through manufacturing and to delivery are defined by routes.
Setup:
- Make to Order: The production of goods takes place only after receiving customer orders.
- Make to Stock: Produce and keep products in stock based on demand forecasts.
- Drop Shipping: Directly deliver products from supplier to customer.
- Multi-step Routes: Configure complex routes involving multiple steps (e.g., quality checks, staging).
Benefits:
- Optimized supply chain management.
- Reduced lead times and stockouts.
- Improved production planning and efficiency.
Key Functionalities in Odoo for Toy Manufacturing
Bill of Material (BoMs)
Functionality:
- Add BoMs: For each toy, BoMs list all required components and raw materials, including their quantities.
- Work Orders: Generated based on BoMs, work orders facilitate efficient planning and scheduling of production tasks.
- Workstation Allocation: Assign work orders to specific workstations or machines for organized manufacturing.
Benefits:
- Streamlined production planning.
- Clear tracking of materials and components.
- Enhanced organization and workflow management
Inventory Management
Functionality:
- Tracking: It will be possible to keep track of raw materials, work-in-progress, and finished goods.
- Automated Reorder: Never let the stock run out as a result of applying reorder rules.
- Inventory Report: Help with understanding the stock levels, movements, and valuation.
Benefits:
- Prevents stockouts and overstocking.
- Maintains production continuity.
- Provides accurate inventory data for better decision-making.
Quality Control
Functionality:
- Quality Tests and Inspections: Set up tests at various production stages to ensure product quality.
- Compliance: Ensure toys meet safety and quality standards.
- Issue Tracking: Record and address quality issues promptly.
Benefits:
- Maintains high product quality.
- Enhances customer satisfaction.
- Ensures compliance with industry standards.
Challenges
- The major challenge is the testing part in toy manufacturing (The QC parameters are unique per product and specific)
- Logistic management is also a key challenge to maintaining the number of components and their reordering
Configuration at One Place
- Navigate to Products:
Go to Inventory > Products > Products. - Create a New Product:
Click on Create to add a new finished product. - Set UOM:
In the General Information tab, select the primary UOM, Purchase UOM, and Sales UOM. - Define Sales Price:
In the Sales tab, set the standard price and configure price lists if needed. - Add Variants:
Add attributes and their values in the Variants tab to generate product variants. - Configure Routes:
Select applicable product routes in the Inventory tab based on your supply chain requirements.
Example Scenario: Toy Manufacturing Company
Imagine a toy manufacturing company setting up a new finished product, "Action Figure".
UOM: The primary UOM is "piece". The purchase UOM is a "box" (containing 12 pieces), and the sales UOM is also a "piece".
Sales Price: The standard price is set at $20 per piece.
Routes: The product follows a "Make to Stock" route to ensure availability for immediate shipment. Additionally, a drop shipping route is configured for large wholesale orders.
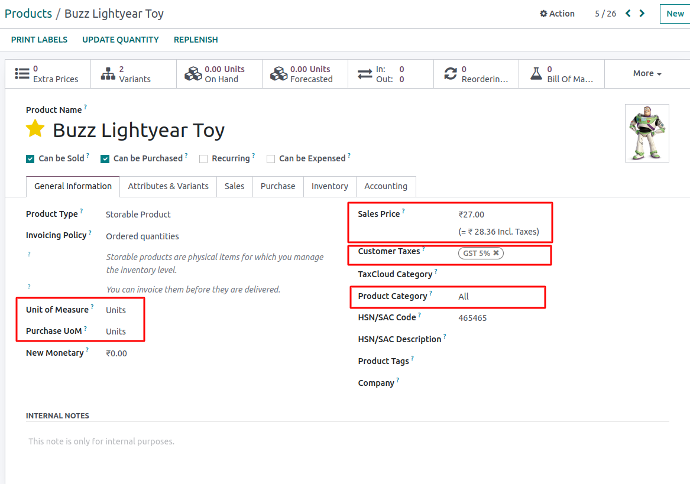
- Multiple Variants & Attributes
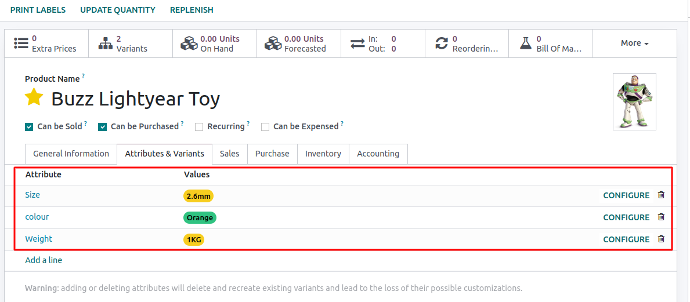
- Multiple routes management
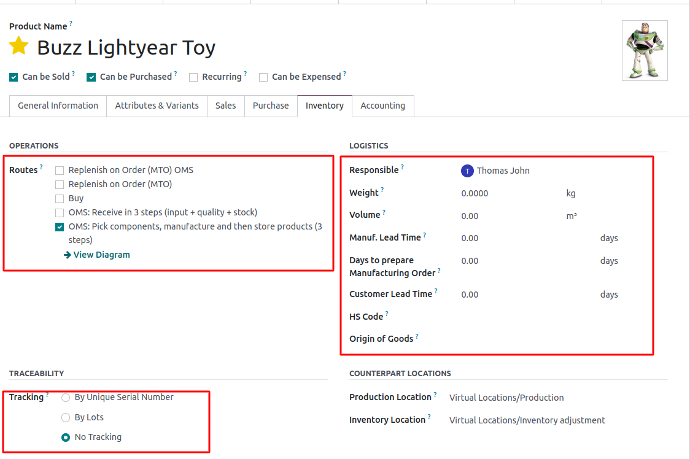
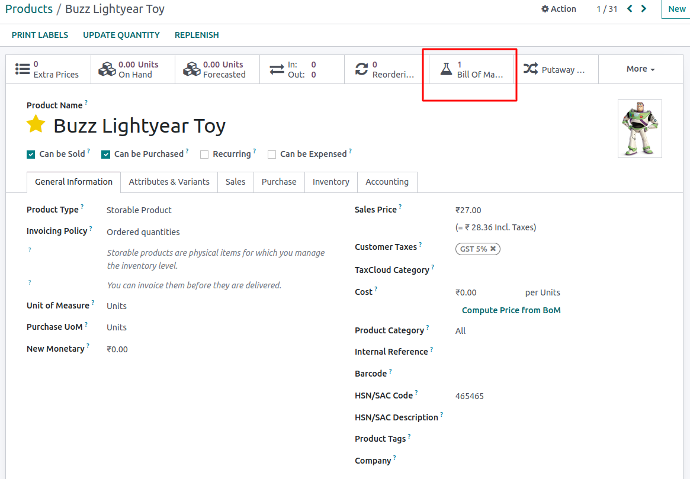
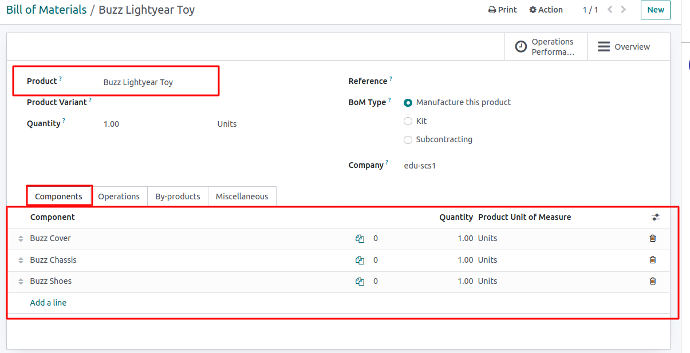
1. Set multiple Operations
Based on the Bill of material we have provided the option to set multiple operations, their duration, Work center defining, and computation method, and can add Worksheet
Functionality:
- Set Operations: Define multiple operations based on BoMs.
- Duration and Work Center: Set operation durations and assign work centers.
- Computation Method and Worksheet: Add computation methods and worksheets for detailed guidance.
Benefits:
- Detailed operation management.
- Efficient workflow setup.
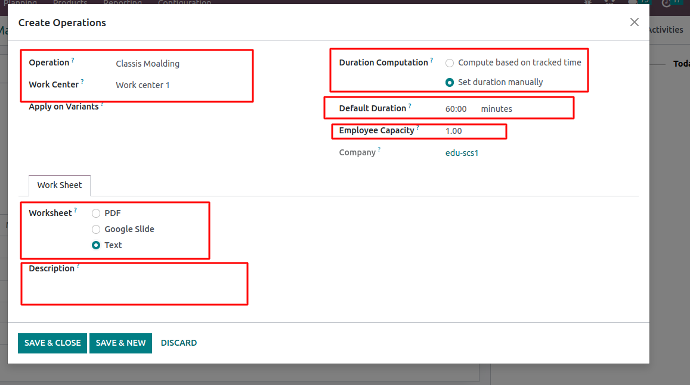
2. Real-time duration
- We can easily measure the real-time manufacturing duration and status of all the operations
Functionality
- Measure Duration: Track real-time manufacturing duration and operation status.
Benefits
- Accurate tracking of production times.
- Enhanced production efficiency.
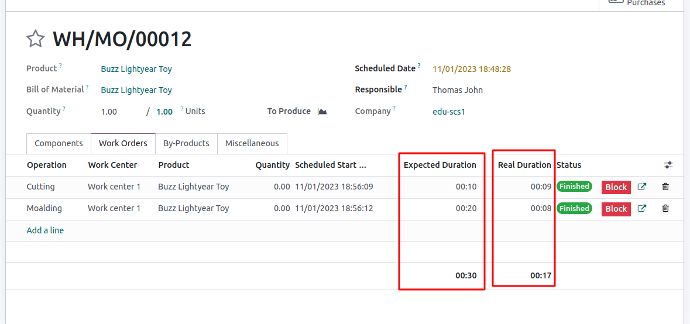
3. Cost Analysis
- Can easily analyze the cost of operation and cost of components to track the real-time manufacturing cost
Functionality
- Analyze Costs: Track operation and component costs to determine real-time manufacturing costs.
Benefits
- Improved cost management.
- Helpful in decision-making for sale price.
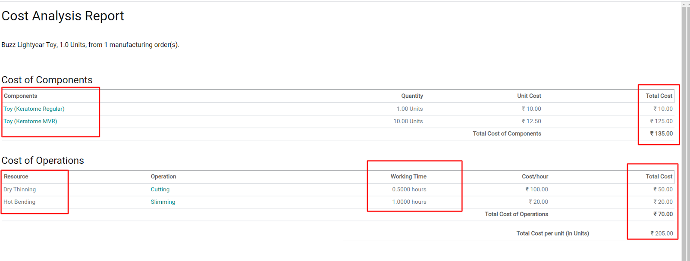
4. Reporting
- Production Analysis - We can conveniently observe product production across different weeks represented in Pie charts, Line charts, and Bar charts. These visual representations serve as valuable tools for making informed decisions in the future.
Functionality
- Production Analysis: Observe production trends across weeks using visual representations like pie charts, line charts, and bar charts.
- Overall Equipment Effectiveness: Measure work center effectiveness and productivity.
- Manufacturing Orders: View cumulative totals of manufactured products.
Benefits
- Informed decision-making.
- Improved equipment utilization.
- Comprehensive production tracking.

Overall Equipment Effectiveness - We can easily measure the equipment effectiveness of different centers and its productivity - Fully productive time, Material Availability, Equipment failure
Manufacturing orders - This report will display the cumulative total of manufactured products up to the present.
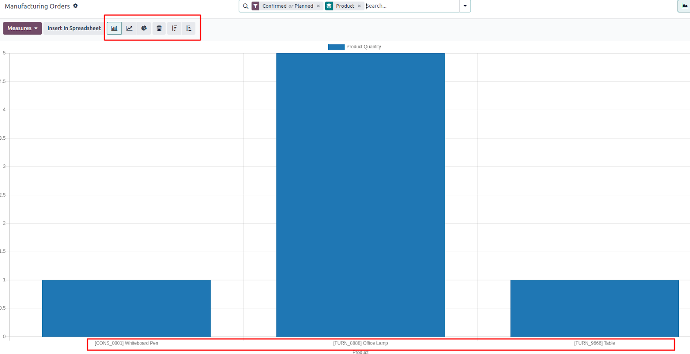
Conclusion
Odoo offers an integrated solution for toy manufacturing, covering all aspects from production planning to quality control. With its extensive features and customizable options, Odoo ensures efficient management of manufacturing processes, contributing to higher productivity and product quality.